Noble Dairy Grants Pass Oregon Sell Ground Beef
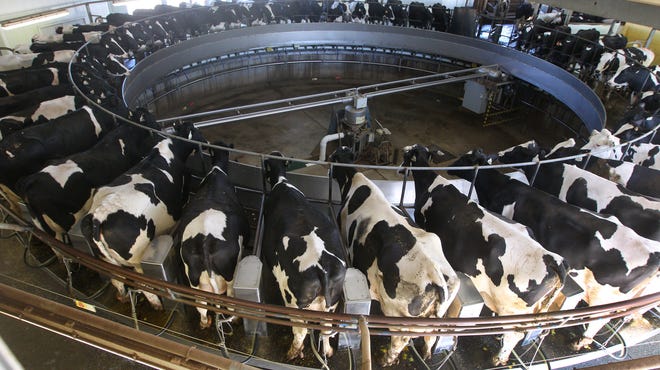
At Noblehurst Farms in Livingston County, cows are raised and milked, barns are mucked out, and manure is spread on fields as fertilizer.
What isn't so obvious about this long-standing operation in the York hamlet of Linwood are the cutting-edge agricultural techniques at play. Creating energy with manure; employing sex-screening veterinary technology to impregnate cows exclusively with female calves, since males aren't needed on a dairy farm; using a new type of on-farm milk processing that could disrupt the traditional way dairy producers market and sell their milk.
It's a place where cows get a 10-minute ride, three times a day, on a milking carousel that runs around the clock. Some like it so much, they have to be led off to allow other Holsteins to take their spots.
And in an era where it's tough to persuade young people to pursue agriculture, Noblehurst called home one of its own — an MBA banker who left New York City to create innovative, green ventures down on the farm.
To get in a place where Noblehurst could support such initiatives, it had to be innovative in the way it made money. Since the 1960s — when the current farm president's grandfather, Ken Noble, was in charge — the farm has suggested, encouraged and joined in partnerships with other farms. Pooled resources save on costs and generate greater profits.
While many farms own businesses like trucking companies to control costs, Noblehurst goes far beyond the norm.
Noblehurst Farms is a holding company whose 30 shareholders comprise multiple members of the Noble and Klapper families, as well as non-relatives.
The company oversees or is invested in:
• Two other large-scale dairy farms.
• Linwood Management Group, an agricultural consulting and management company.
• Linwood Turf Equipment, a landscaping equipment dealership.
• Linwood Commodities, a buying group for cattle feed and straw.
• Noblehurst Green Energy, an entity to produce power from the gases produced by bio-digested manure and other organic wastes.
• Natural Upcycling, a company that composts pre-consumer food wastes.
• Craigs Station Creamery, a milk plant under construction at Noblehurst's heritage farm, will cold-process milk and cream they hope will be sought by — and more valued by — yogurt plants and other dairy processors. The plant is scheduled to open Sept. 1.

The creamery is unique in two ways: It's the first plant in the state dedicated to cold milk separation, and it's the only partnership of large-scale milk producers in the milk-processing end of the business in western New York.
"They were an early adopter on some of the anaerobic digestion," said Tom Overton, director of the Pro-Dairy program at Cornell University's College of Agriculture and Life Sciences. (Noblehurst's first manure digester was destroyed by fire in 2011. A much larger biodigester, which will power the new milk plant, is under construction now.) Some dairy farms might compete with or surpass Noblehurst for innovation in one area, he said, but few if any are as innovative across the board.
"They always have an eye on the bigger picture: not only what's going on in the Northeast that could be affecting the dairy industry, but also on a national or even global" basis, Overton said.
One area in which Noblehurst is pushing ahead in is the type of opportunities it creates for its young people.
"Very few businesses survive past the third generation," said John Noble, president of Noblehurst Farms. Often by the time the third generation comes along, the business hasn't expanded exponentially to support them or provided new challenges to keep them interested. The traditional way for farms to support new generations is by adding cows and acreage, he said.
Noblehurst has done that, swelling to 2,400 acres under cultivation and 1,600 cows milked. But it also diversified with an eye toward giving younger family members and partners attractive reasons to stay on the farm.
"They're bringing them back in ways that add new elements to the business as opposed to directly within the core of the dairy business," Overton said.
For the farm's first four generations, John Noble said, the family fed its members and made money by farming. But his grandfather, Ken, brought the farm from horses to tractors, from single operators to farms partnering to buy more modern, expensive equipment and consolidate and expand their herds.
In the 1960s, the farm began diversifying, a tradition continued by Ken's son, Jack, and grandson, John.
John's son, Chris Noble, walked in the footsteps of at least three earlier generations of Nobles by getting a degree or certificate at Cornell University, where John is a trustee. But Chris worked in banking in New York City before he got his MBA at Cornell's Johnson School of Business.
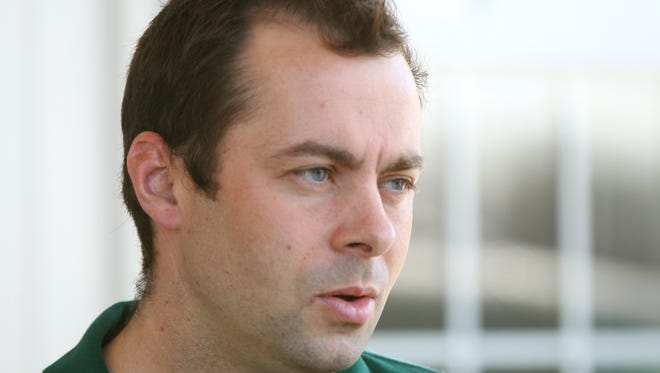
"Agriculture hasn't been traditionally thought of as being the highest-paying or sexiest job to come back to," Chris Noble said. "One of my dad's big initiatives is providing ways for young people to thrive in agriculture."
Work in the farm's management consulting company and the chance to begin new ventures — he started the food-waste composting business a few months ago — helped lure Chris back to the family homestead full time in 2009.
"You have to keep your eyes open to what the next generation can bring," said Sarah Noble-Moag, Chris' aunt and John's sister. A shareholder and secretary of the board, she handles human resources and training for the approximately 120 people employed by Noblehurst and its enterprises.
Cows are still at the center of everything Noblehurst Farms does.
One barn near the family homestead houses about 1,400 heifers: young cows that haven't had a calf yet. Another houses about 1,600, nearly all of whom are milking. A third location about three miles away is where the calves are raised, fed by bottle on milk produced at the farm.
On a chilly, rainy day visit to the farm, the barns seem surrounded by a sea of mud, an impression heightened by the two projects under construction. On a later visit, when the sky is clear and the sun is blazing, the dirt driveways are dry and the surrounding fields are a lush green. But warmer weather also makes the unmistakable odor of dairy farming more obvious.
The cows inhabit two huge, open-sided metal barns. Each barn has a wide aisle running down the middle, bordered by piles of cow feed. Hundreds of cows stick their heads through railings to munch on the mixture of hay, corn and other elements designed to maximize milk output. As the cows push their noses through the pile, it tends to drift toward the center of the aisle. A worker driving a little tractor will push the feed back toward the cows when it gets too far away.
Several times a day, workers who come from this area, Mexico or the central Asian country of Bhutan guide groups of cows to the milking parlor. Once inside that building, the cows walk onto an elevated carousel with 50 slots holding them still. The animals travel around the circle with their heads toward the centers, udders aiming outward.
As soon as a cow enters the carousel, one worker douses its udders with disinfectant. A second wipes them off, tugging on each teat to help start the flow of milk. A third places a contraption that looks like a four-legged spider on the teats, each "leg" a suctioning tube. Once the cow's udder is emptied, the device flies off and the cow typically shifts her back legs to get out of the way of the milker.
About 10 minutes after getting onto the carousel, the cow's teats are given a coating to prevent infection in the barn and the animal is guided off the carousel. It walks back to the barn, where it will eat and sleep some more until the next milking time.
Each cow has identifying tags on its ears and a radio tag on one leg that is scanned to let the farm record how much milk it gives and how many steps it takes — the latter an indicator of health or readiness to be impregnated again.
Traditionally, farmers get paid for their milk according to a complicated national formula heavily weighted toward the way the milk will be used. If the milk goes into a bottle for drinking, that's the highest price. If the milk is used to make yogurt, the price is slightly lower. If it is used to make cheese, which has a longer shelf life, the price is lower still. And if the milk isn't used for any of those and has to be made into powdered milk, the price is even lower. The quality of the milk also can earn the farmer some premiums.
The formula also takes into account the location of the farmer and, in this region, the distance from Boston. Farmers in western New York, for instance, earn about $1 less per hundred pounds of milk than farmers in the suburbs in Boston.
Livingston County farmers get paid about 10 cents more per hundred pounds than those a little to the west, so the location of the Noblehurst Farms is key. One hundred pounds of milk equals about 12 gallons.
This fall, the farm expects to start operation of Craigs Station Creamery, a joint venture of eight local farms and the Dairy Farmers of America co-op. The farms will all bring milk — 1 million pounds a day — to be cold-processed there. The idea is to separate the milk in a way that doesn't strip milk proteins of some of their characteristics. The creamery also adds some attributes that a growing number of consumers are starting to demand: "It's local, it's green (powered by a manure digester), it's fully traceable," Chris said.
The Nobles are betting they can get a premium from yogurt-makers and other dairy processors for their cold-processed milk. Plus, for each hundred pounds, they'll save pennies on hauling costs, which will add up quickly on 1 million pounds a day.
Under the traditional marketing plan, "farmers aren't typically allowed to get closer to their consumers with their product," John Noble said. "What we're doing is disruptive."
A few years ago, state and federal grants enticed some New York farmers to invest in biodigesters as a partial solution to what to do with their manure.
Farm operations have grown so much that their manure's environmental and nuisance issues aren't always dealt with successfully by the traditional methods of collecting waste and spreading it on fields as fertilizer.
Biodigester systems basically turn manure into three products, one of which can be used to generate electricity. The system allows the manure, along with some food wastes, to percolate for about 30 days in a closed tank with an expandable lid. As bacteria digest the manure mixture, methane gas — the smelliest part of the manure — is made and collected. The gas becomes fuel to run an electrical generator.
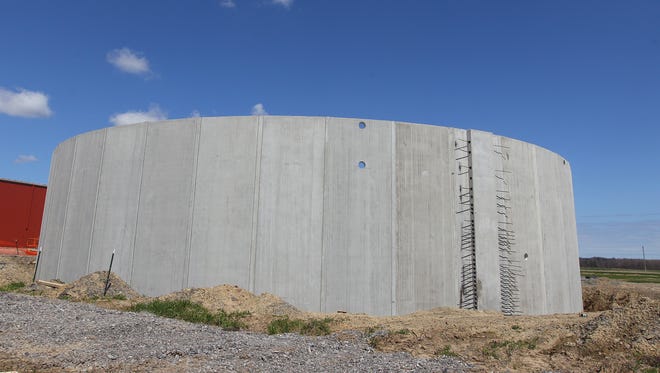
The other two parts are solids and liquids. The liquid — now a lot less offensive — is still trucked to fields and spread on the ground to fertilize crops. The solids, also not smelly anymore, are dried and usually used as bedding for the cows who make the manure.
As soon as the first biodigesters came on line, what to do with all the electricity became an issue, as they generally produce more power than a single farm can use. And New York's electrical grid wasn't entirely equipped to accept a lot of power from varying sources around the state.
"We talked about ways to use biogas," said Chris Noble, management consultant with one of Noblehurst Farms' enterprises, Linwood Management. "Maybe a greenhouse to grow tomatoes?"
One might ask, what do tomatoes have to do with dairy farming?
"We're very much an entrepreneurial company. Our mission statement doesn't say anything about dairy or cows," Noble said.
Noblehurst's original 135-kilowatt biodigester was one of the first in the state, but also the first to suffer a major setback; it was destroyed by fire in 2011.
The family-owned farm is building a 440-kilowatt biodigester now. The concrete tank is 100 feet in diameter and 30 feet deep, sunk about 10 feet below grade. Total cost: $3.2 million, including a $497,520 federal grant. It should be ready this summer.
A generator of that size can provide enough power for 300 homes. But Noblehurst intends to use the power to run the barns and houses on the heritage farm, and its newest venture, which isn't tomatoes after all.

Perhaps to no one's surprise, the venture ended up being related to dairy: a 14,000-square-foot, $12 million plant called Craigs Station Creamery, which will separate cream from dairy in a little-used cold process, retaining the original structures of the proteins. Eight farms partnering in the plant project will bring their milk to be processed at this plant. Dairy Farms of America, a giant dairy co-op, is a 60 percent investor.
The investors hope to recoup their investment by cutting transit costs for their milk and by generating value-added milk products that Western New York yogurt and ice-cream makers will find attractive.
What: A holding company for several agriculture-related businesses stemming from a seven-generation family-owned dairy farm and its partners.

Key players: John Noble, president; Christopher Noble, Rob Noble and Tim Klapper, all vice presidents; Sarah Noble-Moag, treasurer; Roberta Klapper, secretary.
Locations: Main farm is in the hamlet of Linwood, in the town of York, Livingston County. Other land holdings are in nearby Genesee and Wyoming counties, with additional enterprises in Covington and Attica, both in Wyoming County.
Employees: 120 across the various businesses that Noblehurst owns and part-owns, 40 of whom work on the original farm. Twelve of the 30 shareholders work for the farm and its affiliates.
How Noblehurst measures success: In jobs created that allow its young people to continue in the family business, in developing sustainable ventures that support the farm, employees, owners and community, developing new consumer products.
Noblehurst in a word: diversified.
About this business
Noblehurst Farms is the ninth company to be featured in our Passport to Innovation series. It's noteworthy because:
• The multigenerational, multifamily farm business is unusually diversified, including a farm management consulting company, a lawn equipment dealership, a commodities buying group for animal feed, and an energy company based on composting manure and food wastes.
• Noblehurst, in a partnership with local farms and a national dairy co-op, is moving into dairy processing by building a new kind of milk processing plant at the farm.
bradfordhatessuce.blogspot.com
Source: https://www.democratandchronicle.com/story/money/business/2014/06/05/noblehurst-farms-passport-innovation/10017145/